---------------------------------
코킹콜, 코크스에 관심있는 분들은 한번 읽어 보세요. <포스코 뉴스 펌>| 석탄 정보.토론방
카페지기 | 조회 515 |추천 0 | 2011.07.14. 00:28
다특성 석탄 혼합한 코크스 제조 ‘세계 최고’저가탄 사용 50%이상 확대 목표로 기술개발
왜 요즘 많은 사람이 석탄에 열광할까? 1950년대 중동에 대규모 유전이 개발되며 사람들에게 가장 친숙한 열원 자리를 석유에 내준 지 60여 년이나 지나 요즘 왜 다시 석탄에 대한 관심이 커지고 있을까? 가장 큰 이유 중 하나는 매장량이다. 석유의 매장량은 최대 3조 배럴로 추산되는 데 비해 석탄의 추정 매장량은 10조 톤으로 석유의 26배에 이른다. 또한 석유는 습곡작용을 받은 지층의 산봉우리처럼 불룩하게 올라간 부분에 모여 있는데 석탄은 가혹하지 않은 조건에서 물길을 따라 생성되며 크게 편중되어 있지 않다. 따라서 호주·캐나다·중국·유럽·인도네시아 등 전 세계에 걸쳐 다양한 종류의 석탄이 채굴된다. 심지어 우리나라도 삼척 등지에서 채탄되며 매장량은 약 15억 톤에 이른다. 또한 기술 발달로 석탄의 이용범위가 넓어지고 있는 것도 큰 이유다. 종전엔 활용하지 못하던 석탄을 손쉽게 채굴해 자원화할 수 있는 기술이 지속적으로 개발되고 있다. 석유수출국기구(OPEC)가 석유의 가격과 공급량을 장악하고 있는 상황에서 석탄을 이용해 에너지 자립도를 높인다는 것은 굉장히 매력적일 수밖에 없다.
 |
▶ |
▲건식소화설비(CDQ: Coke Dry Quenching) 버킷(Bucket)에 적재된 적열 코크스. | |
다양한 종류의 석탄 = 석탄을 나누는 방법은 번개탄과 연탄 등 용도에 의한 분류만 있는 것이 아니다. 석탄은 크게 3가지 기준으로 나누는데 첫 번째가 탄화도, 두 번째가 순도, 세 번째가 타입이다. 첫 번째 기준인 탄화도는 석탄이 얼마나 오랫동안 석탄화되었는가를 표시하는 지표이고, 이에 따라 크게 이탄·갈탄·아역청탄·역청탄·반무연탄·무연탄 등으로 나눈다. 두 번째 기준인 순도는 불순물인 재(ash)와 황(sulfur)의 함유량이 얼마인지를 나타낸 지표이며 가격 결정에 바로 영향을 미친다. 마지막 기준인 타입은 석탄이 어떤 식물로부터 왔는지를 나타내는 지표다. 예를 들면 단단한 침엽수에서 석탄화된 것과 부드러운 활엽수에서 석탄화된 것의 품질은 크게 다르다. 이를 분류하기 위해 현미경 관찰을 사용하며 분류 기준이 되는 조직을 마세랄(maceral)이라 한다. 이렇게 3가지 기준으로 분류하는 석탄은 워낙 다양한 식물이 탄화된 것이기 때문에 같은 지역, 같은 탄광에서도 품질이 똑같다고 할 수 없다. 따라서 석탄의 구조를 일일이 파헤치는 원소분석보다 현미경 관찰 마세랄 분석을 주로 실시한다.
석탄 사용방법에 따른 분류 = 이러한 석탄 분류 이외에도 사용하는 방법에 따라 발전용 탄이나 코크스(coke) 제조용 탄으로 나눌 수 있다. 발전용 탄은 말 그대로 석탄을 직접 태워 열을 냄으로써 고압 스팀을 만들고 발전기를 돌리는 데 사용한다. 모든 석탄은 탄소를 주성분으로 하기 때문에 발전 용도로 사용할 수 있으며, 우리나라만 보더라도 코크스 제조용 석탄의 2배 이상을 발전용 석탄으로 수입하고 있다. 다른 하나는 코크스 제조용 석탄이다. 코크스 제조용 석탄은 간접 가열하면 매우 뻑뻑한 액체 상태로 변하는 성질이 있는데, 이 같은 상변이 현상을 이용해 분 상태의 석탄을 덩어리 모양의 코크스로 만든다. 모든 석탄에 이러한 성질이 있는 것이 아니라 일부 석탄만이 뻑뻑한 액체로 변하는 성질을 지니고 있으며, 역청 같은 액체 상태를 갖는다 해서 역청탄이라 부른다. 이 석탄은 땅속 깊숙이 매장돼 있으며, 수요 대비 공급이 부족하기 때문에 가격이 높게 형성된다.
제철소에서 석탄의 사용 = 제철소에서 사용하는 석탄은 앞에서 이야기한 코크스 제조용 역청탄과 고로 PCI(Pulverized Coal Injection)용 탄, 그리고 소결용 무연탄이 있다. 코크스는 고로의 위로부터 철광석과 함께 차례로 들어가 열을 내어 철광석을 녹이고 고로 밑으로 슬래그(slag) 형태로 빠져나온다. 코크스가 단단해야 아래로는 용융된 철광석이 잘 내려가고 위로는 열풍이 잘 올라간다. 코크스로(coke oven)에서 역청탄을 사용, 간접 가열해 코크스를 만드는데 이 과정에서 나오는 가스(gas)를 정제해 제철소의 열원인 COG와 고부가가치 부산물인 타르(tar) 및 조경유를 생산한다. 다른 하나는 고로 PCI용 탄이다. 고로에 열을 공급하는 방법은 위로부터 코크스를 넣는 방법 외에 밑으로부터 열풍과 함께 파쇄된 석탄을 넣는 방법이 있다. 짧은 기간에 충분히 잘 타야 하므로 얼마나 파쇄가 잘되는지와 얼마나 높은 열량을 가지고 있는지가 중요하다. 폐가스가 대기 중에 방산되지 않고 가스 형태의 열원으로 회수되기 때문에 넓은 범위의 석탄을 사용할 수 있다. 마지막으로 소결용 무연탄은 분광에 열을 가해 소결광을 만드는 과정에서 분광에 섞어 열을 주는 용도로 사용되며, 발열량이 높아야 하고, 직접적으로 태우면서 발생한 폐가스를 굴뚝을 통해 배출하는 공정이기 때문에 질소산화물(NOx)의 저감을 위해 질소 성분이 낮은 무연탄이 선호된다.
제철소별 원료사용 패턴 = 제철소에서 석탄을 사용하는 방법은 제철소의 위치에 따라 다르다. 먼저 광산에 인접한 제철소는 인근 광산의 석탄과 철광석을 주로 사용한다. 일 년 내내 2~3개 탄종의 석탄을 끊임없이 사용하며 후공정 또한 2~3개 탄종이 만들 수 있는 코크스 품질수준에 맞춰 조업한다. 이 경우 광산에 대한 제철소의 의존도가 높아 몇 십 년 동안 장기 계약을 맺거나 상대방의 지분을 보유하고 있는 경우가 대부분이다. 다른 하나는 대부분의 원료를 수입해 가공하는 방식으로, 원료와 제품을 수송하기 위해 해안에 위치해 임해 제철소라 불린다. 포스코 또한 임해 제철소인데 원료 공급의 안정성과 경쟁력 강화를 위해 가능한 한 많은 공급처에서 다양한 종류의 원료를 공급받는 것이 특징이다. 따라서 광산이 폭우나 폭설로 생산에 차질을 빚으면 전자인 광산에 인접한 제철소의 경우 생산을 중지할 수밖에 없지만 후자인 임해 제철소의 경우 다른 공급처를 통해 생산을 지속할 수 있다는 차이가 있다. 통상 임해 제철소는 8~9개 탄종을 섞어 코크스를 만들고 가능한 한 많은 양의 석탄을 보유하고 싶어 한다.
석탄 배합기술 = 코크스 제조기술의 시작은 석탄 배합기술이다. 앞서 이야기한 것처럼 석탄은 품질과 특성이 너무 상이해 비슷한 곳에서 생산된 석탄을 바꿔 사용했을 뿐인데도 코크스 품질이 크게 달라진다. 석탄 간에도 궁합(宮合)이 존재하는데, 평소엔 좋은 품질의 코크스를 생산하지 못하는 석탄이라도 궁합이 잘 맞는 석탄과 함께 사용하면 플러스 알파의 품질을 낸다. 물론 반대의 경우도 존재한다. 또한 산지와 종류도 매우 다양해 어떤 석탄은 이송 시 분진이 많이 날리고, 또 다른 석탄은 코크스로에 손상을 주기도 한다. 더욱이 석탄은 실험실에서 제조한 코크스와 실제 코크스로에서 생산한 코크스가 다른 조직을 보이는 것으로 유명하다. 실제로 모르는 석탄이 입하될 때 품질에 대한 가장 정확한 분석은 그 석탄을 코크스로에 사용한 경험이 있는 다른 제철소에 물어보는 것이다. 여러 가지 석탄을 섞어 사용하는 임해 제철소에선 각자의 상황에 맞춰 석탄 배합기술이 최적화돼 있으며, 경쟁력 보호를 위해 어떤 석탄을 얼마만큼 섞어 사용하는지는 비밀로 하고 있다. 포스코는 일 년에 약 40개의 서로 다른 종류의 코크스 제조용 석탄을 사용하며, 통상 석탄 야드(yard)엔 약 20개의 석탄더미(coal pile)가 사용 또는 사용 대기 중에 있고, 한 번에 10~14개 탄종을 섞어 코크스를 제조한다. 또한 활발한 광산 투자와 공급 다변화를 통해 매년 5개 이상의 신규 석탄을 실 조업에 적용 중이다. 석탄 배합의 노하우 지표라 볼 수 있는 실제 코크스에서 사용한 석탄 브랜드 수는 단연 포스코가 세계 최고다.
저가탄 사용 요구 = 제철소의 경쟁력을 강화하는 방법은 값싼 연료를 사용해 좋은 품질의 제품을 만드는 것이다. 석탄의 가격은 품질에 따라 천차만별인데 점결성이 높아 좋은 코크스를 만들 수 있는 강점탄의 경우 매우 비싸며, 품질이 낮고 수분을 많이 함유하고 있는 갈탄의 경우 강점탄 가격의 10분의 1 수준이다. 코크스 제조용 석탄 중에서 점결성이 매우 낮아 스스로 코크스가 되기 힘든 저가의 석탄은 미점탄 또는 저가탄으로 분류된다. 하지만 혼자서는 코크스를 만들 수 없는 미점탄도 어떤 석탄과 섞어 어떻게 사용하느냐에 따라 좋은 품질의 코크스를 만들 수 있다. 또한 대부분의 고품질 원료광산을 주요 공급사가 독점한 상태에서 포스코의 신규 석탄 광산 개발 투자는 품질이 낮은 석탄에 집중될 수밖에 없다. 따라서 저가의 미점탄을 다량 사용하면서 높은 강도의 코크스를 제조하는 기술에 우리 포스코의 미래가 달려 있다고 해도 과언이 아니다.
기술개발 과정 및 효과 = 임해 제철소의 단점이자 장점은 원료를 외부에 의존하기 때문에 다양한 종류의 석탄을 사용해야 하며, 배합을 자주 바꿔줘야 한다는 것이다. 배합비를 변경할 때마다 코크스 품질은 흔들릴 수 있기 때문에 불안한 반면 다양한 석탄을 활용해 고품질의 코크스를 만들 수 있다는 점에선 장점이다. 포스코에선 안정적인 원료 확보를 통한 경쟁력 강화를 위해 다양한 석탄 광산에 적극적으로 투자하고 있다. 원료구매그룹과 화성부 간 신규 석탄에 대한 의견을 공유해 가격과 품질을 고려한 평가가 이루어진다. 또한 세계 각지에서 생산되는 석탄의 특성을 파악해 최적으로 배합을 맞추는 일은 기술연구원과 현장에서 가장 우선적으로 실시하고 있다. 어떤 석탄이 어떤 특성이 있기 때문에 어떤 석탄과 함께 사용해야 좋은 품질의 코크스를 만들 수 있는지를 파악하기 위해 수많은 테스트가 지금도 진행되고 있으며, 이렇게 쌓인 노하우는 고품질 코크스를 만드는 기초가 됐다. 이 같은 노력으로 2006년 이전 20%를 밑돌던 저가탄 사용 비중은 현재 40% 이상으로 비약적인 향상을 보이며 포스코 원가절감에 큰 기여를 하고 있다. 몇몇 석탄 수분을 극한적으로 낮추는 설비를 갖춘 제철소를 제외하고 동일 설비 기준 포스코의 저가탄 사용 비중은 자타가 공인하는 세계 최고 수준이다.
최고를 유지하기 위한 노력 = 최고의 철강 기술력 확보와 경쟁력 강화를 위한 노력은 지금도 지속되고 있다. 저가탄 사용 비중 40%에 만족하지 않고 50% 이상 사용을 목표로 석탄의 수분을 추가적으로 낮추고 인조 점결제를 첨가하는 등 장기적인 관점에서의 기술개발이 진행 중이다. 석탄이라는 재료를 혼합해 코크스라는 고로가 먹는 최고의 음식을 만드는 예술작업은 오늘도 계속되고 있다.
윤석호 yoonish@posco.com<자료=선강기술그룹>
 |
▶ |
포항 코크스공장 로상(Oven Top) 전경. | |
 |
▶ |
코크스 오븐에 구워진 적열 코크스(사진 왼쪽)와 고로로 이송되고 있는 건식 코크스. | | |
----------------------------------------------
Met Coal 101
Coal is formed from plant remains that have been covered by a layer of sediment and are subjected to geological forces over time. The forces of the sediment overlaying the plant material cause chemical changes that create a carbon rich substance know as coal. Coal is a readily combustible black or brownish-black sedimentary rock that is composed primarily of carbon, along with variable quantities of other elements such as sulphur, hydrogen, oxygen and nitrogen. Based on its properties, coal can be classified by rank, from lowest to highest, into the categories of lignite, sub-bituminous, bituminous and anthracite. Lower rank coals contain less carbon, more moisture and have lower calorific values.
In general terms, based on the rank, coal can be classified as either “thermal” coal or “metallurgical” coal. Thermal coal is lower in carbon content and calorific value, higher in moisture value, is the world’s most abundant fossil fuel and is primarily used to produce energy. Metallurgical coal is less abundant than thermal coal and is primarily used in the production of coke which is an important part of the integrated steel mill process.
Metallurgical coal is primarily sold to steel mills and used in the integrated steel mill process.
When making steel, two of the key raw ingredients are iron ore and coke. Coke is used to convert the iron ore into molten iron. Coke is made by heating coking coal to about 2000°F (1100°C) in the absence of oxygen in a coke oven. The lack of oxygen prevents the coal from burning. The coking process drives off various liquids, gases and volatile matter. The remaining solid matter forms coke, a solid mass of nearly pure carbon. Approximately 1.5 tonnes of metallurgical coal are needed to produce one tonne of coke. only certain types of metallurgical coal have the necessary characteristics required to make coke. These characteristics include caking properties (the ability to melt, swell and re-solidify when heated) and low impurity levels (e.g. moisture, ash, sulphur, etc.).
There are three main categories of metallurgical coal: (i) hard coking coal that forms high-strength coke; (ii) semi-soft coking coal that produces coke of lesser quality; and (iii) PCI coal. PCI coal is generally not considered to be a coking coal, rather it is used primarily for its heat value and is injected into a blast furnace to replace expensive coke. Semi-soft and PCI coals normally have lower sales values compared to hard coking coal due to the relative availability of these products. Integrated steel mills will optimize the use of semi-soft and PCI coals in order to reduce overall costs. However, there are technical limits to the ability of integrated steel mills to substitute semi-soft and PCI coals for hard coking coal in their coking coal blend. During periods of high steel demand, high productivity and high PCI-rate furnaces require higher coke quality, for which more high quality hard coking coal is required.
The following schematic outlines how steel is produced in an integrated steel mill.
The principal market for Grande Cache Coal's hard coking coal is the seaborne hard coking coal market. The seaborne hard coking coal market is defined by the global nature of international steel-making, the relative concentration of quality metallurgical coal deposits in Australia, Canada and the United States and the relative low cost of seaborne transportation. Total worldwide production of higher quality metallurgical coal was reported to be 170 million tonnes in 2010 and expected to increase to 203 million tonnes in 2013. Australia was the largest exporter at 62% while Canada followed at 13%. Australia, Canada and the United States account for 94% of total world seaborne trade.
Trade in the seaborne hard coking coal market is influenced by crude steel production that, in turn, is largely dependent on the overall state of regional and global economic conditions. The global trade of steel products is very large and fluctuations in supply and demand in various regions throughout the world are common. Although there are fluctuations in the total amount of steel produced worldwide, the amount of steel produced by the integrated steel mill process has been steadily increasing, until very recently. In turn, the volume of hard coking coal used in this process has not experienced the same variability as total steel production; however, recent price stratification has, in the short term, resulted in increased volume volatility of hard coking coal used in the process. Canadian hard coking coal is competitive in the seaborne market due to its high quality, its suitability for blending with coking coals from other countries and the desire of steel producers to diversify their supplier base in order to create competition and security of supply.
--------------------------
석탄을 높은 온도로 건류할 때에 얻어지는 잿빛을 띤 구멍이 많은 고체.
코크스 [cokes]
1. 코크스
점결특정 형태의 역청탄을 공기와 접촉시키지 않고 고온으로 가열하여 휘발성 성분이 모두 날아가고 남은 고체 잔류물. 점결탄(粘結炭)의 고온건류에 의해서 생기는 다공질(多孔質) 고체연료로 해탄(骸炭)이라고도 하며, 코크스라는 말은 독일어 Koks에서 온 것이다. 회색을 띤 흑색이며, 금속성 광택을 지니는데 고정탄소가 주성분이며, 회분(灰分)·휘발분을 약간 함유한다. 용도는 제철용 ·주물용 ·가스화용(도시가스 및 화학공업용) 기타로 대별된다. 반 이상은 제철용으로 사용되며, 가정용 연료로는 값이 비싸고 불이 잘 붙지 않으며 잘 타지 않기 때문에 거의 사용하지 않는다.
해탄(骸炭)이라고도 하며, 코크스라는 말은 독일어 Koks에서 온 것이다. 회색을 띤 흑색이며, 금속성 광택을 지닌다. 고정탄소가 주성분이며, 회분(灰分) ·휘발분을 약간 함유한다.
공업분석값은 보통 고정탄소 80∼94%, 회분 6∼18%, 휘발분 0.5∼2%이며, 원소분석값은 탄소 80∼92%,
수소 1∼1.5%, 질소 0.5∼0.9%, 산소 0.4∼0.7%, 황 0.5∼1%, 회분 6∼18%이다. 발열량은 1kg당 6,000∼7,500kcal, 착화온도는 400∼600℃이다. 제조법은 분쇄한 석탄을 코크스로(爐) 안에 장입(裝入)하고, 노벽(爐壁)에서 1,200℃의 온도로 가열하면 노벽에 가까운 부분부터 용해하기 시작해서 분해하여 휘발분을 발생한다.
이 용융상태에 있는 층의 온도가 더욱 상승해서 고화(固化)하여 코크스가 된다. 가열시간을 늘려서 노 안이 전부 코크스화하는 것을 기다렸다가 물을 뿌려 불을 끈다. 보통 16∼24시간에 건류는 끝난다. 노를 가열하는 데는 코크스로가스 ·고로(高爐)가스 ·발생로가스 등을 사용한다. 원료로 사용하는 석탄은 모두 점결탄인데, 석탄의 점결성은 견고한 코크스를 만드는 중요한 성질이다.
일반적으로 강점결탄(强粘結炭) 외에 약점결탄 ·무연탄 등을 혼입하는데, 특히 제철용 코크스를 만들 때는 50∼60 %의 다량의 강점결탄을 혼입한다. 도시가스용이나 화학공업용의 가스용탄에는 대부분 약점결탄을 사용해도 된다. 코크스의 용도는 제철용 ·주물용 ·가스화용(도시가스 및 화학공업용) 기타로 대별된다. 반 이상은 제철용으로 사용되며, 가정용 연료로는 값이 비싸고 불이 잘 붙지 않으며 잘 타지 않기 때문에 거의 사용하지
---------------------------------------
철을 생산하기 위해서는 원료탄과 철광석이 필요하다.
고로 안에 원료탄과 철광석을 집어넣었다고 생각해보자. 열풍을 가하면 가루형태의 원료탄이 날리면서 철광석이 녹는 것을 방해하고 엉켜붙게 될 것이다.
이것을 막기 위해 원료탄을 고로에 들어가기 전 작은 덩어리 형태로 쪄주게 되는데 이것이 코크스다.
세계 최초로 코크스를 이용해 용선을 얻어내는데 성공한 건 에이브러험 다비 1세이다.
그와 그의 동업자들은 1709년 콜브룩데일의 제철소에서 이 코크스 용선법을 성공시켰으며 이는 곧 영국을 비롯한 여러 나라로 확산됐다.
석탄을 원료로 산업혁명를 이끈 영국은 코크스를 통해 양질의 철을 대량 생산할 수 있게 됐으며 점차 놋쇠 등의 구리 합금이 강철로 대체됐다.
철을 녹이는 원료가 목탄에서 석탄, 그리고 코크스로 대체되면서 비로소 철의 대량생산이 가능해졌다고 할 수 있다.
코크스는 점결성 석탄을 코크스로에 넣고 밀폐해서 1천200℃의 온도로 가열해 만든다.
하역된 원료탄은 각 산지별로 야드에 적치됐다가 벨트 컨베이어로 운반돼 일정한 크기의 입자로 분쇄된다.
파쇄된 원료탄은 배합조에서 각 특성에 따라 적정비율로 배합된 후 콜빈(Coal Bin)에 저장된다. 그 후 장입차가 원료탄을 받아 코크스 오븐에 장입하면 약 16시간동안 건류과정을 거친다.
높은 온도로 수분이나 휘발분이 가스로 방출되고 이 상태에 있는 층이 더욱 높은 열을 받게 되면 고화(固化)되면서 코크스가 완성된다.
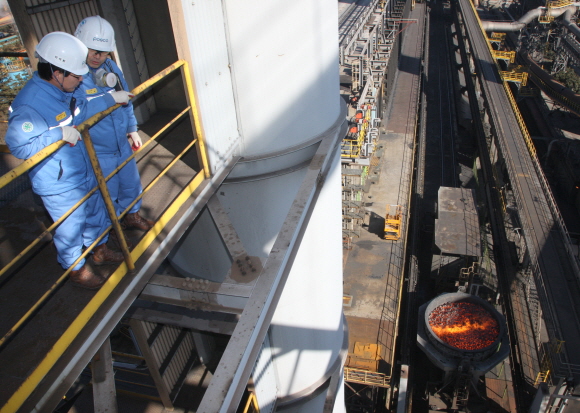 |
▲ 포스코 포항제철소 내 3코크스 건식소화설비(CDQ) 전경. 우측에 코크스노에서 건류과정을 거친 코크스가 보인다. [사진제공 : 포스코] |
압출된 적열코크스는 소화차에서 소화과정을 거침으로써 최종 코크스로 완성돼 고로에서 사용 가능한 것과 그렇지 못한 것으로 분류돼 각각 고로와 소결 과정의 원료로 쓰이게 된다.
소화방식에는 소화탑에서 물을 뿌려 소화하는 습식 소화법과 밀페된 공간애 질소를 불어넣어 소화하는 건식 소화법이 있다.
코크스를 만들기 위해서는 보통 16~24시간동안 가열하며 건류과정에서 발생하는 가스는 화성공장의 정제공정에서 불순물을 제거한 후 에너지센터의 가스저장조로 보내져 제철소의 중요한 에너지원으로 다시 사용된다.
제철용 코크스를 만들 때는 50∼60%의 강점결탄을 다량 혼입하는데 석탄의 점결성은 견고한 코크스를 만드는 중요한 성질이 된다.
고로 안에서 코크스는 철광석을 녹이는 열원으로서의 역할과 철광석을 환원시켜 산소와 쇳물로 분리시키는 역할을 한다.
즉, 열풍으로 코크스가 타면서 일산화탄소를 만들어내고 일산화탄소는 환원성이 매우 큰 물질로 산화철을 환원시켜 순수한 철을 만들어 낸다.
코크스는 제철용도로만 사용되는 것은 아니다. 화학 공업용, 가정용, 비철금속 제련용 등 광범위하다.
최근에는 용기 플라스틱 재활용에 제철용 코크스가 이용되기도 한다.
신일본제철은 플라스틱을 코크스에 장입해 열분해해 이때 나온 석유성분이 다시 플라스틱 제조에 사용하고 코크스는 제철 원료로, 가스는 발전용으로 투입한다.
용기 플라스틱에는 염소가 포함돼 있어 일반적으로 재활용시 설비 부식 방지를 위해 탈염 공정이 필요하지만 제철용 코크엔 염소를 무해화하는 성질이 있어 별도의 공정이 필요치 않다는 게 신일본제철의 설명이다.
한편, 코크스는 제철과정에서 필수적인 원료원이지만 제철산업에 녹색바람이 불면서 코크스 제조공정에서 발생하는 대기오염 물질이 문제가 됐다.
포스코는 지난해 6월 세계 최초로 연산 200만t 규모 파이넥스 공장을 착공했다.
파이넥스 공법은 철광석이나 유연탄의 별도 가공할 필요없이 가루 형태의 철광석과 유연탄을 바로 사용하기 때문에 소결공정과 코크스제조공정에서 발생하는 황산화물(SOx), 질소산화물(NOx), 분진 등 환경오염 물질을 줄일 수 있다.
파이넥스 공법은 투자비와 원료 가공비를 절감하고 오염물질 발생을 획기적으로 줄인 혁신 제철기술로 평가받고 있다.
---------------------------------
화성 (코크스)공정
1 . 현황
화성공정은 고로에서 사용하기 적합하도록 석탄을 건류하여 코크스를 제조하는 공정이다.
코크스는 고로와 소결공장의 연료로 쓰이며, 코크스를 제조하는 과정에서 발생하는 부산물
인 코크스 건류가스(Coke Ov en Gas : COG)는 제철공정의 연료로 사용된다.
포항제철소는 1973년 4월 21일 연간 생산능력 58만 4,000만톤의 1코크스공장을 가동하였
다. 이후 대형 고로에 소요되는 다량의 고품질 코크스를 생산하기 위해 4차에 걸친 설비확
장을 통해 1983년 6월 20일에는 연간 530만톤의 코크스를 생산할 수 있게 되었으며, 1989년
1월 9일에는 코크스 누계 생산량 5,000만톤을 기록했다. 1975년 이후 원료탄배합 기술을 향
상시킴으로써 원료탄의 공급선을 다변화 했고, 1978년에는 일반탄의 사용비율을 높이기 위
해 성형탄 제조설비를 설치하고 1988년과 1989년에는 2코크스공장에 건식소화설비(CDQ)를
설치하는 등 지속적으로 설비를 합리화했다. 1989년에는 노체의 수명을 연장하기 위한 최신
보수기술을 개발했고, 1989년 연소관리자동화 등을 적극 추진하여 품질이 우수한 코크스를
저렴하고 안정적으로 생산할 수 있는 기술을 확립하였다.
광양에서는 1987년 4월 연산 143만톤 규모의 코크스 설비를 최초로 준공한 이후 차례로 4
개의 공장을 가동하여 연산 572만톤의 코크스를 생산하고 있다. 특히 대형고로에서의 고출
선비를 유지하며 미분탄 취입조업에 필요한 고품질의 코크스를 공급하기 위해 지속적으로
원료탄 배합기술과 연소 관리자동화 COG탈황기술을 개발하는 등 고로 조업을 원활히 하도
록 하고 있다.
2 . 설비
코크스 제조공정에서는 원료탄 건류에 소요되는 에너지의 사용을 최소화하면서 코크스의
품질을 향상시키고, 원료탄의 비산과 각종 유해물질의 누출에 따른 환경공해를 줄이기 위한
설비를 개선하는데 중점을 두어왔다.
1973년과 1976년에 각각 연산 58만 4,000톤 및 91만 2,000톤 생산규모의 포항 1, 2기 코크
스 설비가 가동된 이후 대형 고로인 포항 3고로가 설치되면서 1978년 11월 준공된 3기 코크
스설비의 생산능력을 연산 155만 2,000톤 규모로 대형화했다. 3기 코크스 설비에서는 유안
제조설비 대신에 암모니아를 분해, 소각시켜 고압증기를 공급하는 폐열 보일러 설비를 채용
했으며, 1979년 2월에는 가격이 저렴한 원료탄 사용량을 늘리고 코크스 품질을 향상시키기
위해 성형탄 제조설비를 준공했다. 또한 1981년 2월에는 4기 코크스 설비를 준공했다.
1983년 6월에는 910만톤 조강생산 체제 구축에 따른 코크스의 안정적인 공급과 고로에서의
보조연료로 사용했던 중유를 대체하고 올코크스 조업을 실시하기 위해 연산 73만 3,000톤의
코크스 설비를 추가로 준공했다. 또한 설비 확장때마다 생산성 증대와 환경공해방지 설비
를 추가한 것이 특징이다.
한편 1987년 3월 30일 가동을 개시한 광양 코크스 설비는 低窒化物(NOx )조업을 위한 연
소실 2단연소, COG의 누출을 방지하기 위한 코크스 노문 자폐(Self Selin g )장치, 분진비산
방지를 위한 시스템(Emis sion Control Sy stem ), 대기 중으로 배출되는 황화물(SOx )을 감소
시키기 위한 탈황설비 등 최신예 공해방지 설비를 갖추고 있다.
○ 화성공장 설비현황
구 분
생산능력
(천톤/ 년)
노 사 양
COG처리능력
(천N㎥/ hr )
탄화실
수(문)
노고(m ) 노폭(m )
포항
1기 584 68 5.0 0.43 32
2기 912 106 5.0 0.43 51
3기 1,552 146 6.5 0.43 88
4기 1,552 150 6.5 0.43 88
4기2차 733 75 6.5 0.43 44
광양
1기 1,430 132 6.7 0.45 85
2기 1,430 132 6.7 0.45 85
3기 1,430 132 6.7 0.45 92
4기 1,430 132 6.7 0.45 92
3 . 조업
1973년 4월 가동을 개시한 포항제철소 코크스 1기설비 초기조업 당시에는 관련산업의 영
세성으로 말미암아 부산물의 처리업체 선정과 원활한 출하에 차질이 생겨 생산에 어려움을
겪기도 했다. 또한 1기 코크스 설비가 가동될 때까지 약 20개월 동안에는 163.5%라는 경이
적인 가동률을 기록했으며, 1977년 4월 24일 발생한 포항 1제강공장 용선유출 사고시에는 1
개월 이상의 장기간에 걸쳐 부분적인 空盧(Banking )조업을 실시하여 코크스로 가동율을
92.3%까지 낮추기도 했다.
1978년부터는 3기설비가 가동되었고 1979년에는 성형탄 설비가 설치되어 원료탄에 성형탄
을 30%수준까지 혼합하여 대형화된 3고로의 고품위 코크스를 공급했다. 1983년 6월에는
포항 4기 2차 코크스 설비의 가동과 더불어 화성공정에서 발생하는 폐수처리를 위해 생화학
폐수처리기술을 적용했으며 1989년 12월에는 포항 2코크스공장에서 코크스의 연소관리를 자
동화하기 위한 기술을 확보함으로써 대형 고로인 포항 3, 4고로 조업의 안정화와 코크스 제
조원가 절감에 기여했다.
한편 1987년 3월 광양제철소 코크스공장이 최초로 가동된 이래 모든 코크스공장에 상승관
리드 자동개폐기, 코크스시료 자동채취기, 고압 암모니아수 분사 자동개폐기 등의 자동화 설
비와 연소관리 자동화, 압출 및 장입 자동스케쥴링, 노온 자동측정 등의 전산화 시스템을 채
용해 효율적인 조업관리를 도모했다. 특히 탄화실 연와 두께가 포항보다 얇은 것을 채용함
으로써 코크스를 제조하는데 들어가는 원료탄 톤당 소비열량을 600Mcal이하로 감소시킬 수
있는 기술을 확립했다. 또한 대형 고로의 고출선비 조업을 유지하기 위해 초기에는 고가인
미탄을 28%수준으로 높게 배합했으나 대체탄종을 개발하여 점차적으로 미탄 배합비를 20%
이하로 낮추어 원가절감을 기하고 있다.
한편 광양제철소 1코크스 설비 가동 초기에는 전면적으로 채용된 자동화설비의 고장이 빈
발하여 정상조업도 달성기간이 길어져 61일이나 소요되었으나 1988년 7월 가동된 2코크스
설비는 1코크스 설비의 경험을 토대로 가동 17일만에 정상조업도를 달성했다. 또한 1, 2코
크스 설비에서 발생되는 COG증가의 황화수소 제거 설비가 가동되었다. 1990년 11월 가동
된 광양 3기 코크스 설비에는 원료탄 장입, 코크스 압출 및 소화차 등의 무인화를 실현했으
며, 가동한지 23일만에 정상조업도를 달성했다.
------------------------------------------
코킹콜 등급 구별 / semi-cokes|질문과 답변
1).코킹콜 시세를 조사하며 아래와 같은 리스트를 작성해봤는데, 요근래 하향 추세네요.
강점결탄 (프레미엄 /스탠다드), 반 약점결탄의 구별 기준은 스펙에서 어떤 factor를 보고 결정하는지 설명을 구합니다.
참고로 최근 러시에서 받은 스펙을 첨부합니다.
첨부 스펙은 어떤 그레이드에 해당될까요?
russia coking coal.zip
코킹콜 (FOB USD) 시세 흐름표
구분 /년도 2008 2009 2010 2011 2012(2) 2012(4)
----------------------------------------------------------------------------
프레미엄 강점결탄 300 129 219 298 235 211
스탠다드 강점결탄 289 120 207 282 222 ---
반 약점결탄 240 83 169 204 162 135
저휘발분 미분탄 245 90 176 215 180 154
-----------------------------------------------------------------------------
2). semi-cokes라고 반성 코크스라고도 부르데요.
통상 900-1200도 에서 가열하여 얻는 코크스가 아니라,
그보다 저온 600도 정도로 가열하여 얻는 코크스라고 하는데 이런 반성코크스를 만드는 이유와
이는 어떤 용도로 사용하게 되는지요?
코크스가 약 $600 /톤 의 시세라면 반성코크스는 얼마 정도의 시세가 될지요?
|
---------------------------------------------
역청탄 [bituminous
연탄(軟炭)이라고도 함.
석탄화 등급이 아역청탄과 무연탄의 중간 정도인 석탄의 가장 풍부한 형태
유럽에서는 발열량이 높은 일부 역청탄은 경질탄(硬質炭)으로 표시되고, 연탄이라는 표시는 발열량이 낮은 역청탄·갈탄·갈색탄에만 제한되어 사용된다.
역청탄은 암갈색 또는 흑색이며, 일반적으로 뭉쳐져 있다. 이것은 95% 이상이 목본(木本) 식물조직에서 유도된 마세랄기인 비트리나이트로 이루어져 있다. 역청탄은 15~35%의 휘발성 물질을 포함하고, 일반적으로 3% 미만의 수분을 포함하고 있어 비교적 높은 열량을 낸다. 역청탄의 이러한 성질과 존재량 때문에, 역청탄은 석탄 중에서 상업용으로 가장 널리 사용된다. 발전소와 산업용 보일러 플랜트에서 증기를 발생시키기 위해 오랫동안 사용되었다. 또한 극소량의 황을 포함하며, 쉽게 깨지는 다양한 역청탄 철광석을 용융시키는 데 중요하게 쓰이는 순수하고 단단한 탄소물질인 코크스를 만드는 데만 사용한다.
코크스는 특별히 고안된 기밀(氣密) 오븐에서 역청탄을 약 1,100℃까지 가열함으로써 생성된다. 이때 석탄은 산소가 없기 때문에 연소되지 못하고, 강한 열이 석탄에 존재하는 많은 휘발성 물질을 기체상태로 방출시킨다.
코크스 제조공정에서 방출되는 몇몇 기체들은 콜타르와 암모니아액으로 압축된다. 역청탄과 관련있는 주요문제점은 공기오염이다. 황함량이 중간 정도 또는 많은 역청탄은 연소되어 공기 중에 이산화황을 방출하고 공기 중의 수분이 이산화황과 반응하여 황산이 된다. 이것은 물방울과 섞여서 산성비가 되어 농작물에 피해를 주고 수질오염을 일으킨다. 이러한 심각한 오염문제 때문에 미국에서는 석탄을 원료로 사용하는 발전소는 황이 덜 포함된 아역청탄을 사용한다.→ 아역청탄